Selective Photoheating for Silicone Optical Bonding on Displays
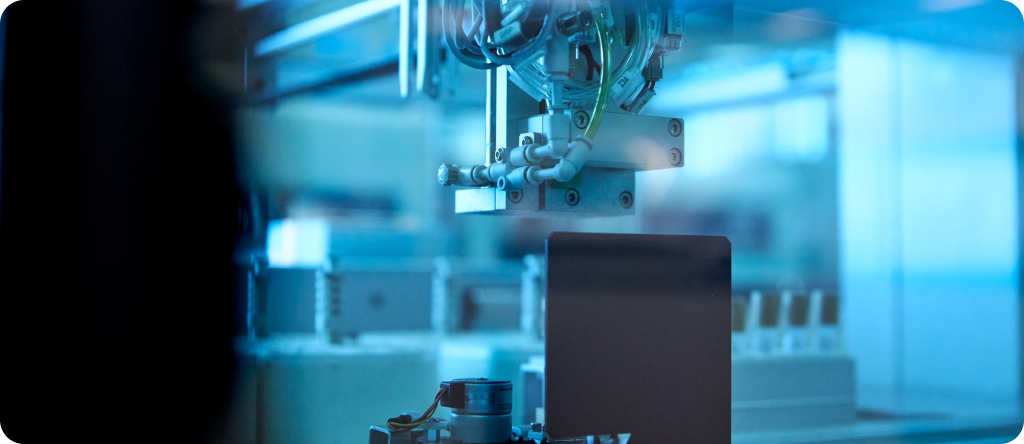
ABSTRACT
IonoQure Limited has developed innovative optical bonding processes that address the challenge of cost-optimized manufacturing of complex optical devices and large display modules.
Selective Photoheating is a new photonic technique resulting from collaboration with technology partners to precisely and effectively cure optical (and structural) adhesives in display applications, suitable for bonding all types of glass/ plastic lenses and substrates.
With this contribution, IonoQure presents a completely new process concept specifically for the optical bonding of displays. The approach enables a slim line design and shows a high degree of flexibility with regard to the mix of component dimensions.
1. OBJECTIVE AND BACKGROUND
Cost pressures, particularly in automotive manufacturing, drive opportunities to refine on new, more efficient processing methods that reduce cycle time and increase throughput and yield.
Working with technology partners from the printing and photonics industries, IonoQure have developed a flexible and efficient process and equipment specifically for the optical bonding of displays, aiming to meet the cost and efficiency requirements of the consumer and automotive industry.
2. APPROACH AND PROCESS DESIGN METHOD
Main driver of an optical bonding process are flexibility, speed, cost, and overall equipment effectiveness. Resin properties, curing method and the interaction of all material-process-equipment parameters have a great influence on the line design.
For maximum flexibility and a lean system design, we have primarily focused on the material application and curing.
The approach enabled us to conceptualize a sleek line design with high flexibility in terms of speed and adaptability to component design and dimensions. In addition, we overcome cure issues in shadowed areas and avoid using an oven or autoclave.
3. RESIN, PROCESS AND EQUIPMENT DESIGN DETAILS
For the process development we have selected a catalytic cure UV-Activated Silicone OCR (Figure 1.).
Viscosity of the OCR is selected so that a layer thickness of 50-300µm can be achieved in one pass.
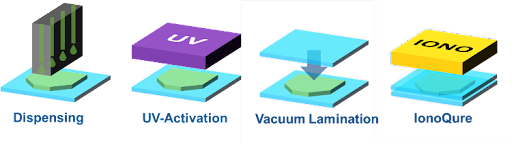
In order to achieve higher yields, we recommend designing a vacuum stage lamination for both processes and types of resin.
For a controlled cure, short name Photoheating (Figure 2.), we have used an apparatus that emits electromagnetic radiation to rapidly increase the temperature to a specified target value and maintain the achieved state within high/ low limits for a specified period of time.
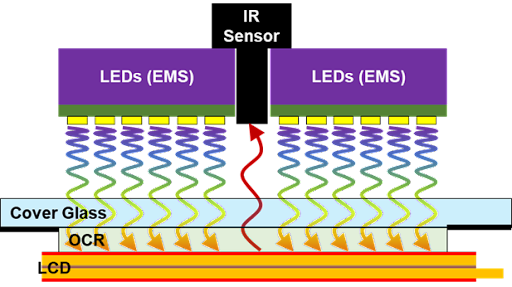
Photoheating causes the Silicone OCR to self-heat by absorbing certain electromagnetic wavelengths. Usually, the heating time is kept within 10 to 20 seconds, and the temperature in the resin is automatically controlled by optical sensors. During the resin heating, there is little or no heating of the surrounding areas and components (measured by ambient temperature sensor).
In Figure 3 below, the temperature developments in the Silicone OCR (blue line) are plotted against the temperature in the gap between EMW-LEDs and cover glass (yellow line). The set target temperature was 70°C (red dotted line).
The EMW-LED driver unit works independently and regulates the LED intensity in closed loop via pulse width modulation (PWM) to keep the temperature as close as possible to the target.
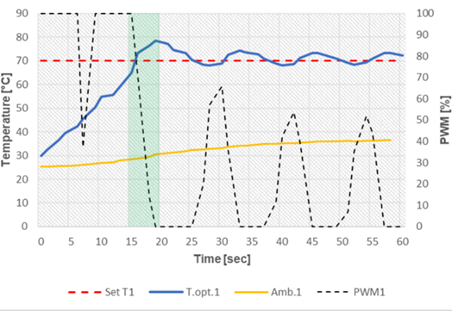
The Selective Photoheating will make a significant contribution to increasing throughput and minimizing the footprint and power consumption of a production line.
4. MEASURING METHOD
To demonstrate the effectiveness of the Photoheating process, we used an UV-Rheometer for the process simulation (Figure 4.). The OCR is enclosed within a glass and POL + OCA (mimicking a typical display module with a cover glass and a LCD).
– Rheometer test setup: Glass/ OCR/ POL
– OCR layer thickness: 500µm
– UV activation: 365nm UV-LED, 4.500mJ/cm², 300mW/cm²
– Target Photoheating-Temperature: 70°C
– Frequency: 1Hz, oscillation mode
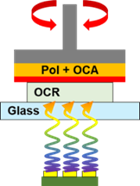

5. RESULTS AND CONCLUSION
Photoheating radiation and measurement starts 60 seconds following the activation with 365nm UV LED.
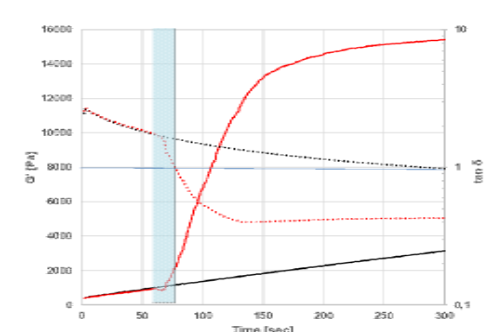
At room temperature, the silicone OCR (black lines in Figure 5.) reaches the gel point after a total of 300 seconds and achieves a storage modulus G’~3.0 kPa.
By using the Photoheating (red lines in Figure 5.) the cure speed is significantly increased compared to RT curing, the gel point time drops from 300 seconds to under 20 seconds and a storage modulus G’~15.0 kPa (5x higher vs RT -Cure).
By conducting pull tests with the same profile as shown above, Photoheating vs. RT pull force values are ~2.5 times higher.
The Photoheating can highly influence the cure profile (speed) and the Silicone OCR bulk material performance.
6. IMPACT
IonoQure Selective Photoheating technique, will significantly influence the development of flexible and efficient processes and manufacturing lines dedicated to optical (and structural) bonding.
Therefore, we will continue the development of suitable processes and materials and intensify cooperation with technology partners.
7. ACKNOWLEDGEMENT
Many of our developments are supported by specialized equipment and technology partner.
8. REFERENCES AND PRIOR PUBLICATIONS
This paper may contain certain forward-looking statements, which are based on internal reports and technical information believed to be reliable.
This content has been previously published.